PressureFit: Leakproof Sprinkler Cap
Overview
This project involved designing a pressure-resistant, leakproof replacement cap for a smart sprinkler head using FDM 3D printing. The cap needed to handle high water pressure, variable outdoor conditions, and material limitations inherent to consumer-grade additive manufacturing.
Problem
-
Layer Line Weakness Under Pressure
Early prints failed catastrophically along layer lines when exposed to pressurized water, especially where vertical splits formed along stress paths. -
Water Sealing Challenges
3D-printed surfaces lack the smoothness and tight tolerances of injection molding, creating persistent leakage issues when threaded or pressed into place. -
Outdoor Durability
Initial prototypes made in PLA warped or cracked under sun exposure and repeated use.
Technical Approach
1. Diagnosing Layer Failure
After observing vertical splits during pressure testing (see Test 1 below), I researched mechanical failure modes in FDM prints. The brittle fracture followed classic anisotropic stress propagation along Z-layer interfaces. I experimented with several solutions:
-
Angled Print Orientations
Rotated the cap on the build plate to redirect stress diagonally across layer lines. -
Support-Driven Redesigns
Introduced internal slants and interlocking geometry to distribute pressure more evenly across multiple print axes. -
Stress-Relief Geometry
Added ribs and reinforced flanges to reduce flexing at stress concentrations.
2. Achieving Water-Tight Sealing
To address leakage:
-
Compartmentalized Pressure Zones
Redesigned internal flow paths to localize water pressure away from seam-critical areas. -
Chamfers & Compression Zones
Added tapering and flexible crush-fit sections to simulate a gasket-like seal. -
Thread Engagement Tuning
Optimized thread depth and spacing to reduce the chance of bypass at threaded interfaces.
3. Material & Environmental Optimization
- Switched to PETG, chosen for its UV resistance, toughness, and reduced brittleness under pressure.
- All designs were validated under real garden hose pressure and multiple thermal cycles.
Development Gallery
Prototype Archive
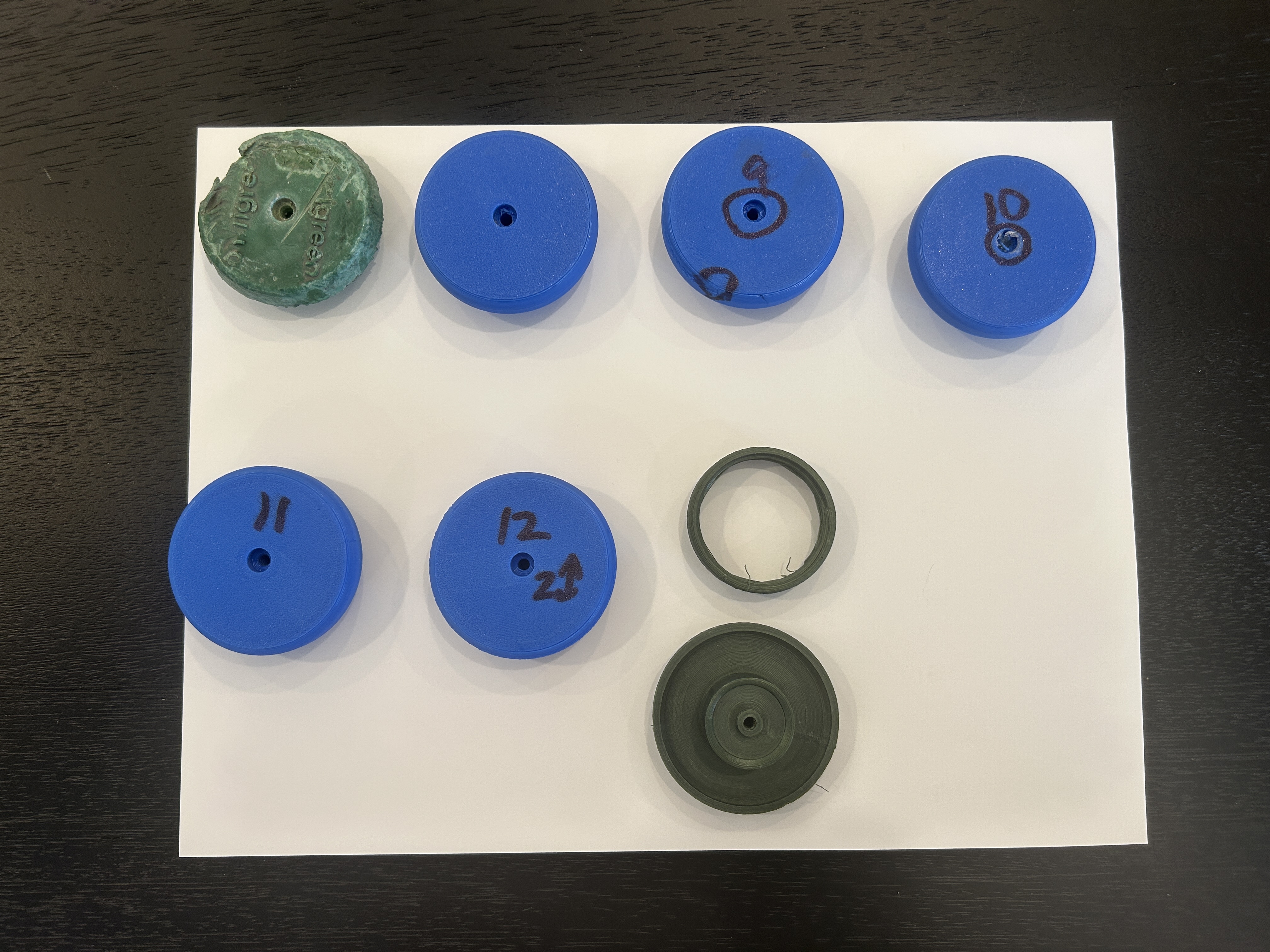
Ten iterations explored seal geometry, thread engagement, material choice, and print orientation. Each change was tested for pressure integrity and outdoor durability.
Internal Compartmentalization
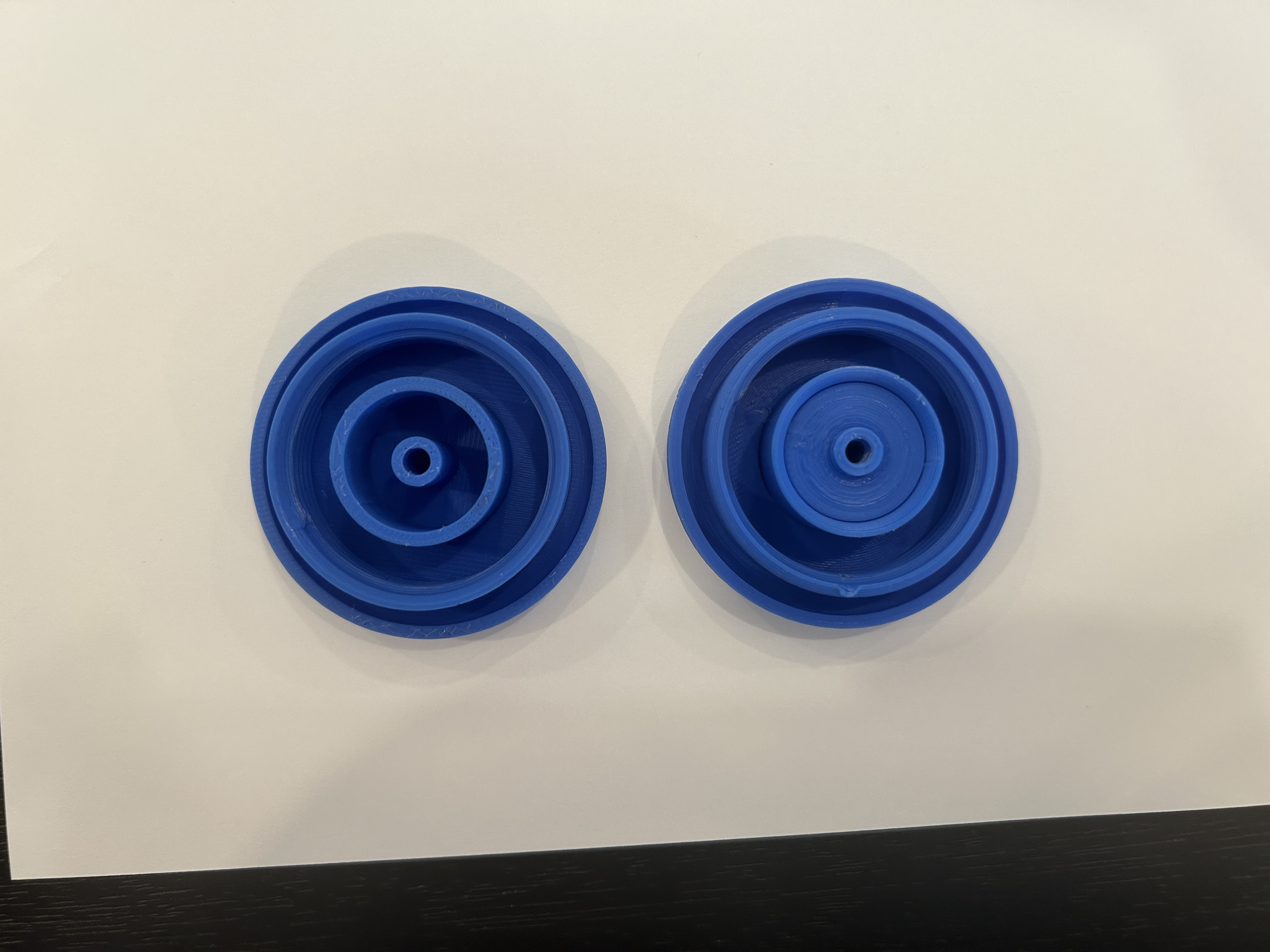
This redesign added pressure-isolated chambers and sealing flanges. It was a key step in eliminating leak paths around the thread root.
Failure Analysis
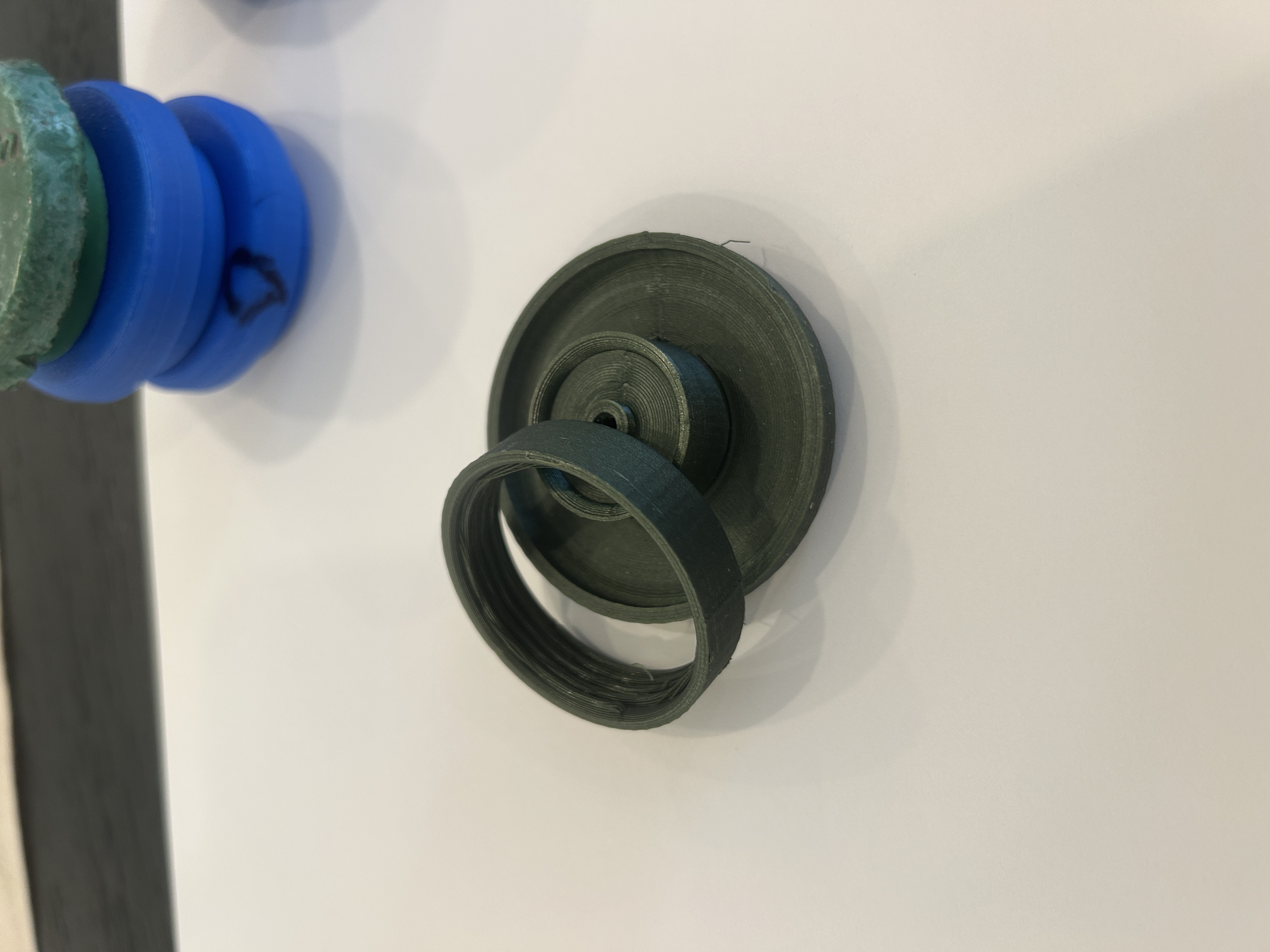
This test revealed vertical failure along layer lines under pressure. It led to angled printing strategies, interlocking geometry, and reinforced sealing zones.
Key Outcomes
-
Researched Print Mechanics to Solve Real-World Failure
Diagnosed and addressed layer-oriented splitting using FDM-specific design strategies. -
Engineered a Leakproof Fit Without Gaskets
Tuned part geometry to take advantage of crush-fit and compression sealing without elastomeric materials. -
Designed for Harsh Outdoor Conditions
Final cap withstood sun, hose pressure, and repeated use without deformation or leakage.
